
The fundamental task of industrial cleaning is to remove contaminants from surfaces, which often include rust, oil, glue, resin or sealants. Traditional cleaning methods, such as chemical treatments, sandblasting or dry ice cleaning, have been used in industry for a long time. However, these methods often produce large amounts of waste, are expensive and have a harmful effect on the environment and human health. Laser cleaning, on the other hand, is a modern and effective solution that has many advantages.
Non-contact and precise cleaning
The essence of laser cleaning is to selectively remove contaminants using high-energy laser light. The process is non-contact, which minimizes the possibility of mechanical damage to the surface to be cleaned, which is especially important for sensitive surfaces where traditional mechanical or chemical cleaning could damage the material.
Chemical-free, environmentally friendly process
While traditional cleaning methods often require chemicals, laser cleaning is a completely chemical-free process, so it does not produce hazardous waste. Laser light removes contaminants directly from the surface, eliminating the need for chemicals that require separate treatment. It is not only cost-effective from a future perspective, but also advantageous from an environmental perspective.
Precise, flexible application
Laser cleaning is used in a wide range of industrial areas, including rust removal, removal of adhesives and sealants, and cleaning of oily and resinous contaminants. This technology is so precise that it can remove contaminants even on complex, hard-to-reach surfaces without damaging the material. The laser can also be easily adjusted to remove only a certain layer thickness, which is especially important in precision industries.
Low maintenance and operating costs
Traditional cleaning methods usually involve a large amount of material consumption, while laser cleaning only requires energy. The non-contact process minimizes wear on the device, which significantly reduces maintenance costs and increases the device’s lifespan, making laser cleaning not only environmentally friendly but also a cost-effective solution in the long run.
Improves the working environment
Laser cleaning does not produce chemical fumes, unnecessary waste or hazardous materials that can be harmful to the health of workers, minimizing the need to handle hazardous materials, creating a cleaner and safer working environment.
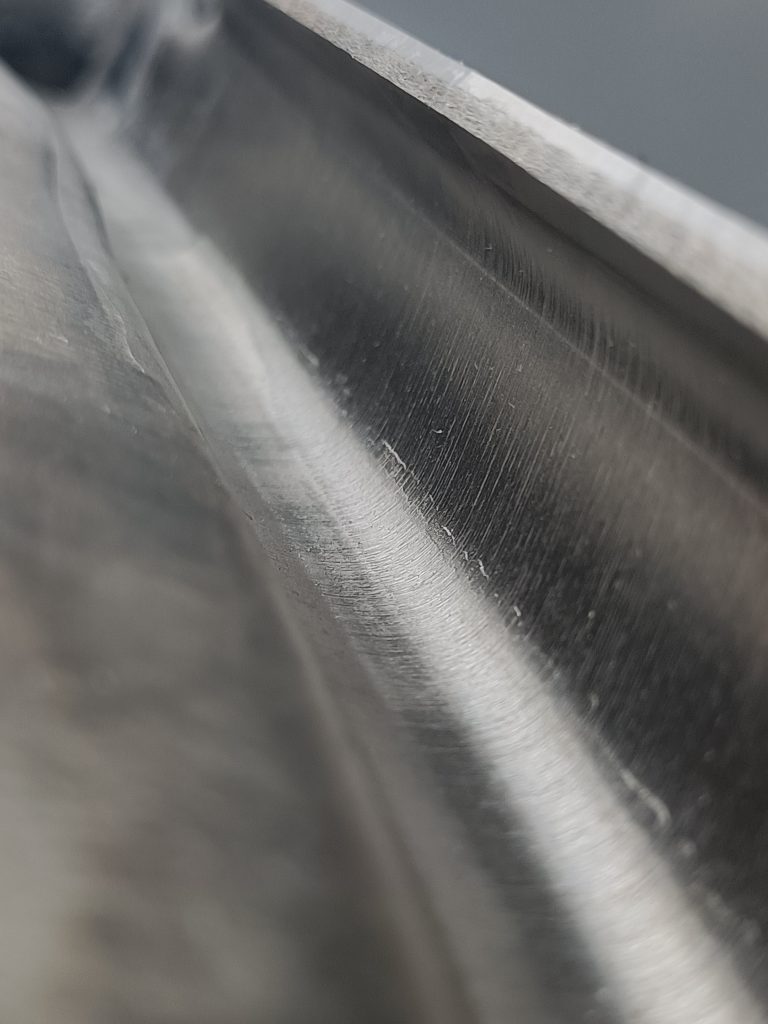
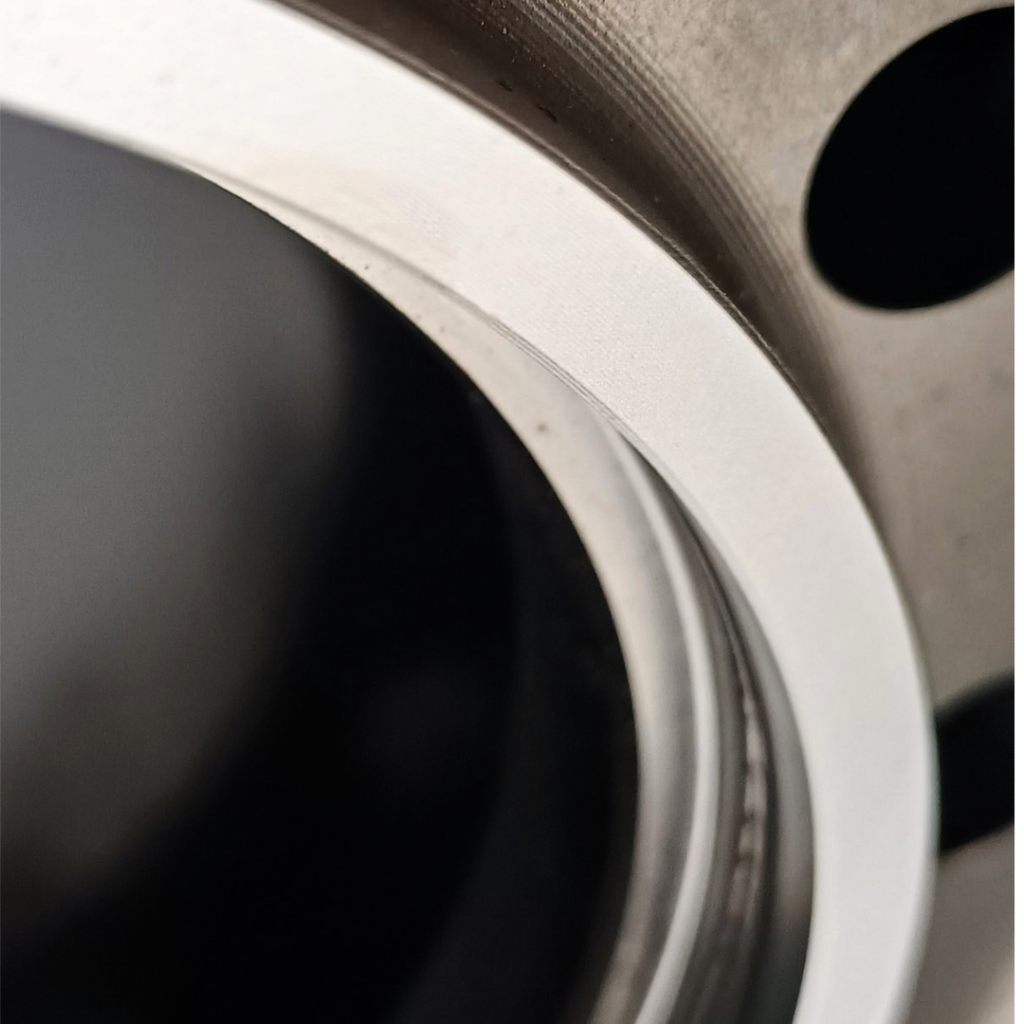
Why choose laser cleaning?
Laser cleaning is becoming an increasingly common solution in manufacturing processes today, as it can effectively remove various contaminants without leaving behind hazardous waste or harmful substances. The technology contributes to sustainability, ensures more cost-effective operations, and creates opportunities to make modern manufacturing processes more efficient.